Babcock was approached by a client who had to replace a main steam piping spherical header due to creep exhaustion of the material (see Figure 1 and Figure 2). This was the result of extended operation at high temperature and pressure. The original design had been done for 100 khr of operation, yet the component was used safely in service for approximately 200 khr. The question naturally arose whether the design could be re-qualified for 200 khr.
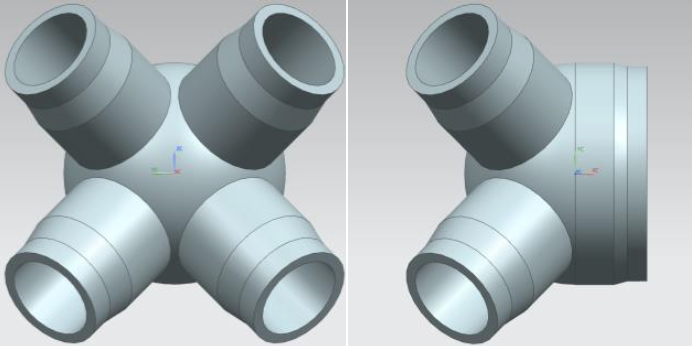
Figure 1: 3-D model of spherical header
The brief
Calculations according to the latest BS EN 13480 design code showed that the design could be used for 120 khr. The client requested that more detailed work be done to qualify the design for 200 khr, if possible. This option was favoured above thickening the component or using more exotic materials. Given its suitability to the problem, Babcock decided to use the Design-by-analysis (DBA) methods of BS EN 13445 in conjunction with finite element analysis (FEA).

Overview of EN 13445 DBA methods
EN 13445 makes provision for the use of design-by-analysis, as opposed to the more commonly used “design-by-formula” approach in codes. DBA uses advanced structural analysis together with acceptance criteria specified by the code to assess the adequacy of a given design. This is done for all relevant failure modes of the component in question. In the case of the spherical header, the following failure modes are important:
- Gross plastic deformation (GPD)
- Progressive plastic deformation (PPD)
- Fatigue
- Excessive creep strain (ECS)
- Creep rupture (CR)
- Creep-fatigue interaction (CFI)
The conclusion
Our client approached us with the need to re-qualify a spherical header for 200 khr of operation where current code formula design allows for 120 khr. It was demonstrated that the design is not suitable for 200 khr, but rather for 141.8 khr. This equates to roughly 3 years of additional operation at 80% plant availability. With the cost of the component at approximately R1.5 million, this is a significant life extension.
Download the detailed whitepaper >>
​Learn more about Babcock's engineering business >>
Figure 2 above: Location of spherical header in piping system